CASE STUDY:
MANAGING NITROSAMINE RISKS IN PHARMACEUTICAL PRODUCTS
01 | The starting point
Review of all chemical and biological human medicines for the possible presence of nitrosamines
as asked for by CHMP
The Committee for Medicinal Products for Human Use (CHMP) asked marketing authorisation holders (MAHs) to review all chemical and biological human medicines for the possible presence of nitrosamines.
Included in this request is the testing of products at risk by following the guidelines.
Companies are now required to have appropriate control strategies in place to prevent or limit the presence of these impurities, and, where necessary, to improve their manufacturing process.
Our client: A global pharmaceutical company
02 | Impact and risks
Our client had already identified 30 products at risk, which meant facing the following consequences:
To avoid the significant impact of these factors, the main task of our team in this project was to maintain as many at-risk products as possible – while balancing the risk of patient safety and economic viability of each product.
03 | Identified challenges
This was compounded by the need for a more efficient and structured storage system to ensure better accessibility and management of project materials.
There was a need to improve visibility and to ensure that all tasks and milestones were clearly documented as well as monitored for better progress tracking.
At the same time, emerging demands from the project team had to be effectively addressed on a daily basis.
This issue had to be addressed to enable smoother project execution.
It required substantial efforts to improve communication and promote stronger, more effective collaboration between departments.
This resulted in significant delays in product testing.
However, through the project, additional laboratory agreements were secured, mitigating this issue. Despite the past delays, no agreements with regulatory authorities were impacted by these capacity constraints.
04 | Our solution as THE FORCE
05 | Key outcomes
of deliverables
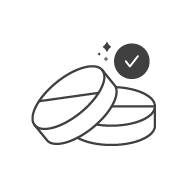
Maintaining product availability
By ensuring the continued availability of affected products, our team was able to safeguard the company's revenue as well as patient access.
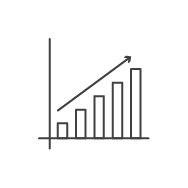
Organisational + operational efficiency
Our team optimised document management and accessibility for nitrosamine evaluations, which benefitted future projects.
In terms of operational efficiency, streamlined processes, improved communication, and defined roles, leading to reduced delays and bottlenecks.
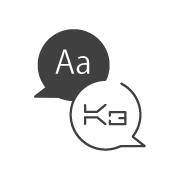
Stakeholder engagement
Through structured meetings and proactive engagement, we overcame initial communication challenges.
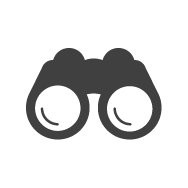
Long-term preparedness
The management process for nitrosamine evaluation established by us equipped our client with a flexible framework to address future regulatory challenges, and now allows them to apply the same approach to other products.
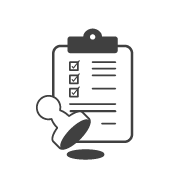
Regulatory compliance
Equipped to navigate regulatory requirements, our team ensured compliance and minimized risks.
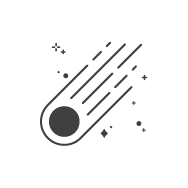
Adaptability
We managed varying risks for each product, maintaining flexibility in timelines while tracking progress effectively.
06 | Long-term benefits
To ensure sustainable compliance when it comes to managing nitrosamine risks in pharmaceutical products, and not least to protect the company's market position moving forward, our final assessment also included recommendations for the future: